UV printer is a common fast inkjet printing equipment in the current market, UV printing has the advantages of fast curing, good resistance, high printing accuracy, and less pollution. More and more advertisers use UV printing to replace traditional printing such as screen printing and offset printing. But UV printing also has an obvious disadvantage in that sometimes the ink is easy to not stick to the substrate, once the problem will greatly affect the product delivery. UV printing ink does not stick to the substrate mainly for the following reasons.
Table of Contents
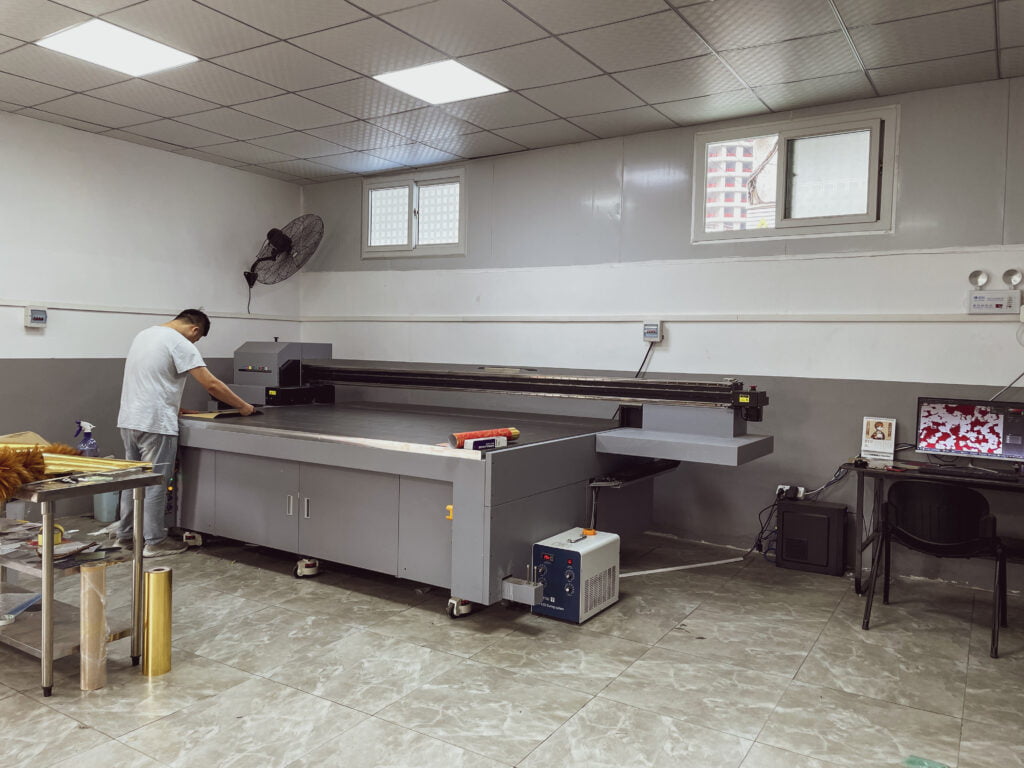
1. UV light power is not enough
Printing ink layer is too thick drying is not complete, UV light power is not enough, light tube aging, light tube reflector aging, UV light output power is too low may cause the ink is not dry and the formation of ink does not stick to the substrate.
Solutions.
(1) the use of deep ink thin printing, deepen the pattern color and reduce the amount of printing ink.
(2) increase the UV light output power, check whether the UV light is aging, regular replacement of UV light, and clean the reflector.
(3) Slow down the printing speed to increase the light time of the ink.
It is worth noting that when the UV light power is too high, it will lead to film-forming ink curl deformation becoming brittle, ink adhesion decreased ink is jagged or block type fall off. At the same time, flatbed UV printers cannot print mirror-like materials (reflecting ultraviolet light) to avoid damage to the printhead.
2. The surface of the substrate is too smooth
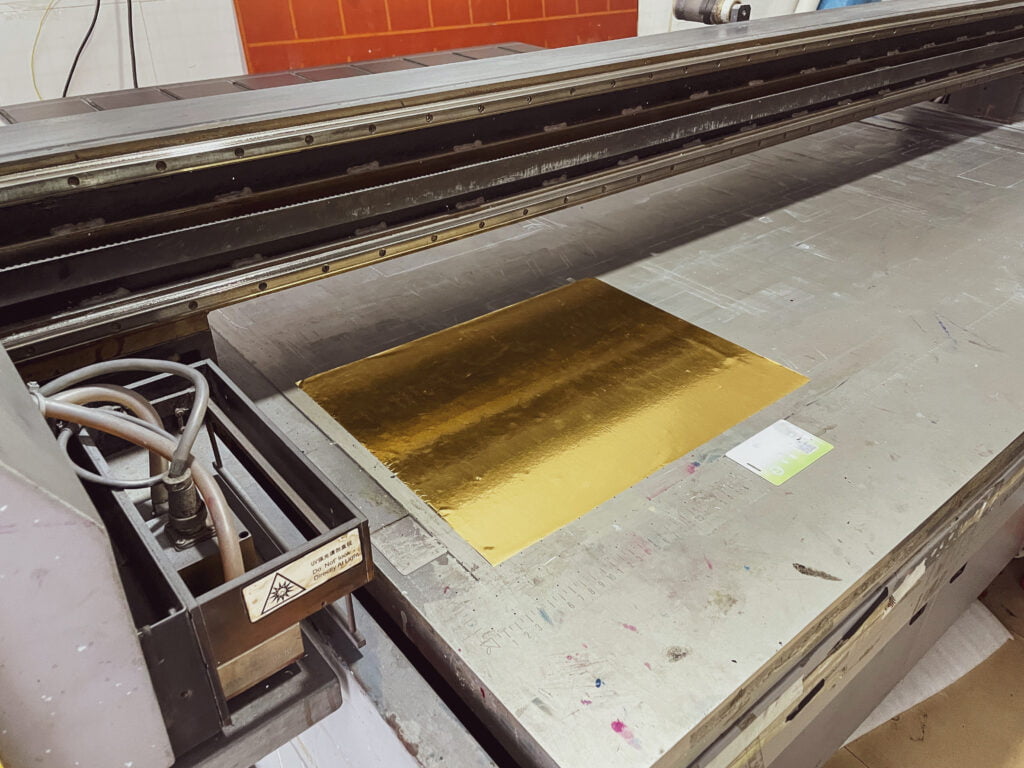
The surface of the material is too smooth, the tension is not enough to reach above 38 darns, and the ink cannot be firmly attached to the substrate surface.
Solution.
(1) Use a satellite rotating machine with an inline corona function and perform inline corona treatment to improve the surface energy of film materials.
(2) Consult with the ink supplier to use a higher adhesion type of ink.
(3) Pre-apply material coating to the material surface before printing.
(4) Replace the material with one that has a surface tension of 38 darns or more.
3. using the wrong ink and material coating
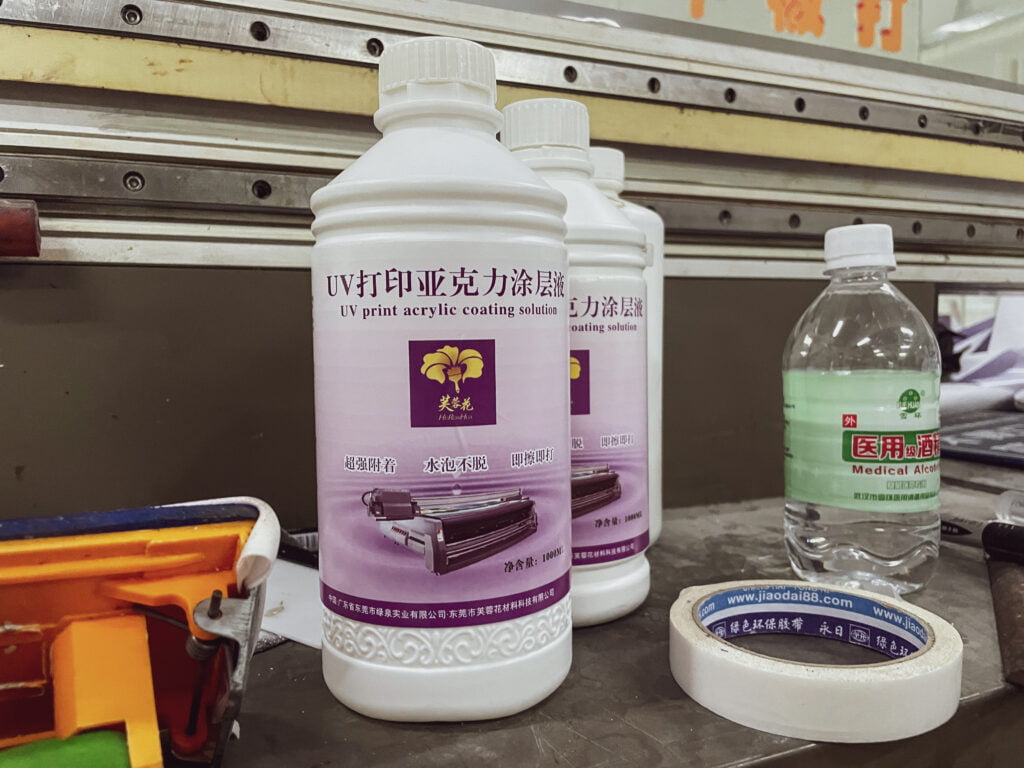
UV printing ink is divided into paper ink, plastic ink, metal ink, frosted ink, special ink, etc. The use of ink does not correspond to the printing on the material will cause the phenomenon of ink loss. Also, there are soft, neutral, and hard ink. The ink printed on the coil needs to use soft ink, otherwise, the ink will break when the material is bent. However, in actual production, there are few UV printers that use soft ink.
The use of material coatings to increase the adhesion of the ink before UV printing is already a mainstream method in factory production. But the coating needs to be selected according to the materials printed, the six common UV printing coatings: metal coating, ABS coating, leather coating, silicone coating, glass coating, PC coating, etc. After printing, it is best to wait for the coating to dry before moving the product to avoid damage to the ink.
4. Ink problems
Ink problems can also cause the ink does not to stick to the substrate, the ink in the light stabilizer is invalid, too much additive more than 3.5%, the ink is expired and the ink is not evenly mixed (print out the ink is powdered fall off)
Solutions.
(1) Purchase good quality UV printing ink, do not mix ink for printing.
(2) replace the expired ink
(3) before printing the ink is fully stirred evenly
The above is our UV printing encounter ink does not stick to the substrate problem, summed up to the solution, I hope to solve your problem.